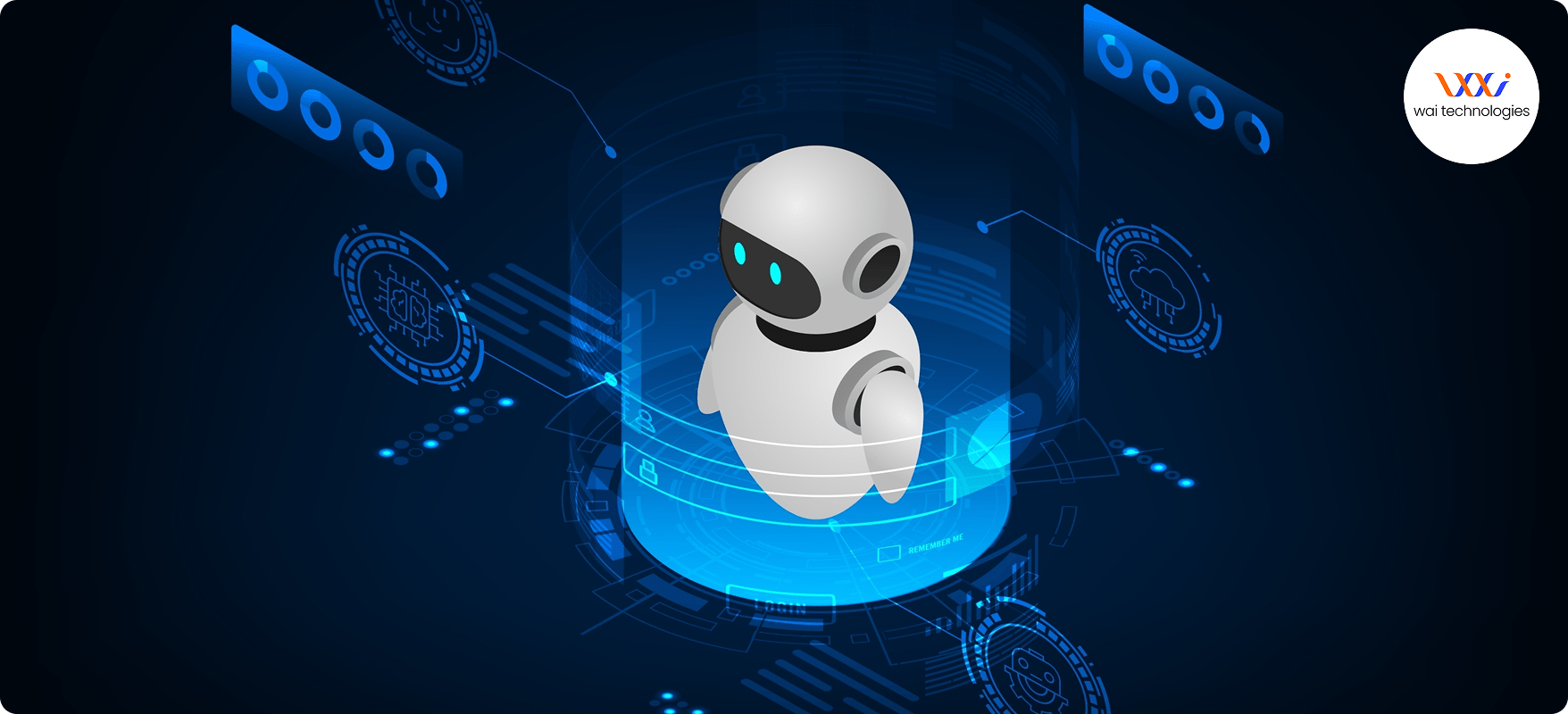
Agentic AI for Predictive Maintenance
Our client, a large US based manufacturer of plumbing products and solutions with manufacturing plants in various locations, transformed its manufacturing operations by implementing an advanced agentic AI system for predictive maintenance across its global facilities.
We developed the system that continuously monitors machinery used in the production of plumbing products, analysing real-time data from precision water control equipment, drainage systems, and bathroom fixture manufacturing lines.
By deploying intelligent AI agents that communicate across facilities, created a network of self-optimizing production systems that predict failures before they occur and autonomously schedule maintenance interventions.
The Challenge:
Prior to implementation, the client faced
- Unpredictable equipment failures causing production delays
- High maintenance costs across geographically dispersed plants
- Inconsistent product quality due to degrading equipment performance
- Difficulty in knowledge transfer between maintenance teams at different locations
Our Solution:
The agentic AI solution operates on three interconnected levels
Equipment-Level Agents
- Dedicated AI agents that monitor individual machines through multi-modal sensors capturing vibration, temperature, acoustic, power consumption, and operational data
- Each agent builds machine-specific behavior models to establish personalized baselines
- Continuous learning improves detection accuracy over time
Facility-Level Orchestration
- Centralized AI orchestrator at each manufacturing location coordinates between equipment-level agents
- Optimizes maintenance scheduling based on production demands and resource availability
- Creates digital twins of production lines to simulate maintenance scenarios before execution
Enterprise-Level Intelligence
- Cross-facility agents identify patterns and insights across all locations
- Enable knowledge transfer of maintenance best practices between facilities
- Provide executives with real-time dashboards showing system-wide health metrics
Technology stack
- AI models: Ensemble models combining LSTM networks, gradient boosting, and reinforcement learning
- Platforms: IoT Core
- Tools: PyTorch, MLflow, Apache Kafka, advanced vibration and acoustic sensors
Implementation Details
The client’s journey to predictive maintenance excellence began with a comprehensive digital transformation of its manufacturing facilities at different locations. The company faced significant challenges with traditional reactive maintenance approaches, especially with specialized equipment used for precision casting, plastic molding, and assembly of complex systems.
Key Innovation: Multi-Modal Pattern Recognition
The system's breakthrough capability is its ability to correlate subtle patterns across different data types. For example, in Client's brass valve production line, the AI detected correlations between minor acoustic anomalies, slight temperature variations, and microscopic changes in material flow that human operators couldn't perceive. This multi-signal analysis provided early warnings of potential failures 3-4 weeks before conventional monitoring systems could detect problems.
Implementation Process
Client rolled out the system in phases
- Pilot implementation at one facility focusing on critical equipment
- Expansion to full production lines with refined models
- Cross-facility deployment with enterprise-level intelligence layer
- Continuous improvement and model refinement based on feedback loops
Impact & Results:
Financial impact
- Savings: Reduced maintenance costs by 24% across all facilities
- Revenue growth: Increased production uptime by 18%
- ROI: 305% return on investment within 18 months of full deployment
Non-financial benefits
- Enhanced equipment reliability: 47% reduction in unexpected downtime
- Improved worker safety: 32% decrease in maintenance-related incidents
- Sustainability: 15% reduction in energy consumption through optimized equipment operation
Results and Future Direction
The implementation transformed Client's approach to manufacturing operations with quantifiable results:
- Maintenance Evolution: Shift from 65% reactive/35% preventive to 15% reactive/45% preventive/40% predictive maintenance
- Production Quality: 22% reduction in quality defects due to early detection of equipment degradation
- Knowledge Management: Creation of an AI-augmented maintenance knowledge base that preserved expertise from retiring workforce
Moving forward, Client wants to expand the system's capabilities to include
- Autonomous self-healing for minor equipment adjustments
- Integration with supply chain systems to automatically order replacement parts
- Advanced scenario planning to optimize production schedules around maintenance events
Conclusion:
By embracing agentic AI for predictive maintenance, Client has positioned itself as a technology leader in the plumbing manufacturing industry, setting new standards for operational excellence and manufacturing intelligence.